NTD: WASHINGTON—The ancient Romans were brilliant engineers and builders, creating a dazzling array of magnificent structures including some that have survived to modern times virtually intact like the domed Pantheon in Rome.
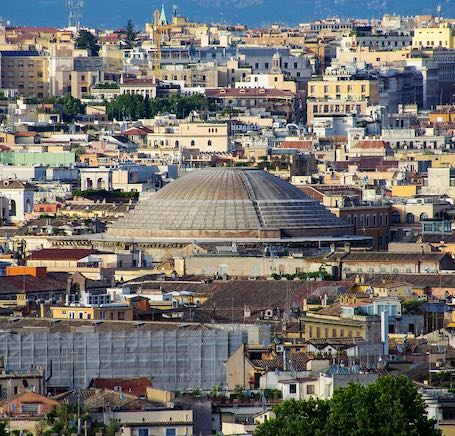
An indispensable material for the Romans was a form of concrete they developed that is known for remarkable durability and longevity, though its exact composition and properties have remained a mystery. A new study goes a long way toward solving this puzzle and, the researchers said, could pave the way for the modern use of a replicated version of this ancient marvel.
Roman concrete was introduced in the 3rd century BC, proving revolutionary. Also called opus caementicium, its three primary ingredients were lime, volcanic ash, and water. It helped the Romans erect structures including temples, public baths, and other big buildings, aqueducts, and bridges unlike any fashioned to that point in history. Because the concrete could harden underwater, it also was vital for constructing harbors and breakwaters.
Many of these structures have endured for two millennia while modern concrete counterparts sometimes crumble in mere years or decades. more
El Diablo, an aqueduct in Spain, still flows water.
The Spanish call it “El Diablo” cuz they couldn’t figure out how it worked and deduced it was the Devil’s work.
Rome collapsed because they allowed their political class to become liars, thieves, and corrupt-o-crats.
mortem tyrannis
izlamo delenda est …
should we be comparing the collapse of Rome to the USA?
no, Rome had good roads
I’m calling Bullshit on this story. That Concrete formula was known then and passed down through the generations. Current engineers didn’t follow it because materials were hard to locate and they don’t want the products they sell to last that long. Duh…
/Salute
I notice a lot of round holes in the concrete exterior of Roman structures. I don’t know exactly why, but I think they attached flat slabs of marble to them and they had to be fixed to the concreter in some way.
Perhaps people ripped off the marble to use them in newer buildings. I don’t know if that’s correct or not. Anybody know?
The Egyptians also had a cement that stood the test of time. The only surviving ingredient is sea water filtered in linen. It makes me think they had the same recipe.
It stood the test of time because they were between a rock and a hard spot.
Me and Corn Pop invented concrete!
That’s all very interesting.
Jimmy Hoffa is wearing roman concrete Galoshes, that’s why he hasn’t been found.
Once you put them on, You cant take em off!
@TimBuktu ~ yes, they pulled off the marble facades. you can see it was extensively done at the Coliseum. if you take the tour, they explain it.
and … @LuvntheBIGsites ~ they knew the formula, but just thought the lime clasts were results of inferior pulverizing techniques … it actually made the concrete able to repair cracks, thus self-healing.
it’s better explained in this article: https://www.science.org/doi/10.1126/sciadv.add1602
with pictures!
The great thing about reinforced concrete is the coefficient of thermal expansion is almost exactly the same for steel and concrete, so with hot and cold cycles, it doesn’t tend to crack around the rebar. Because reinforced concrete hadn’t been invented yet, the crafty Romans made sure their concrete structural members were always in compression.
I worked at Concrete Tech. We did quite a few pontoons for floating bridges while I was working there. We had some mixes that cured up like granite.
1950’s
Construction of the Pilot Plant – first prestressed concrete manufacturing plant in the U.S.
Invention of the Anderson Post-Tensioning System
Development of a family of bridge I-girders – later adopted as WSDOT Standards
Application of internal slip-form mandrel for producing long hollow members
Segmental bridge construction using multi-strand post tensioning tendons
Developed the Decked Bulb Tee Girder which combines a bridge girder and deck as a single precast unit
1960’s
Major plant expansion including construction of 120,000 sf of enclosed production facilities
Cheney Stadium – a design-build minor league ballpark completed in 3-1/2 months
Fabrication of curved prestressed girders for the Seattle Monorail
Testing and acceptance of haunched deck panels and long load bearing piles for heavily-loaded marine piers
Pile-supported prestressed pipe-beams for sewer lines in Lake Washington and Lake Sammamish
Large diameter hollow piles for foundations of major bridges in Washington
1970’s
340 ft. diameter, 20 million gallon capacity Riverton Heights Reservoir Tank for the City of Seattle
Construction of a 150′ x 500′ graving dock and the start of a market for floating concrete structures
Fabrication of guideway elements for the Disney World Monorail in Orlando, FL
Construction of the ARCO LPG Floating Storage Facility; the largest of its kind in the world
165 ft. long, 95-ton girders for the Humboldt Bay Bridge in Eureka, CA
Concrete Technology Associates, a 15 year venture of operating a formal R & D program and testing laboratory
1980’s
Fabrication of 30′ deep x 100′ wide x 700′ long Floating Container Terminal for Valdez, AK
990 bridge girders supporting a landscaped lid over a 1/2 mile section of I-90 on Mercer Island, WA
All-precast 90 ft. tall heavy industrial building for Crown Zellerbach Pulp & Bleach Plant
16,000 pieces of curved tunnel liner panels for the Seattle Metro Bus Tunnel
Six large buried tanks for storing 20 million gallons of JP-5 jet fuel at Adak, AK
Prefabricated floating caisson for a dock at St. Paul Island in the Pribilof Islands (Bering Sea, AK)
1990’s
Construction of 18′ deep x 52′ wide x 930′ long floating bridge drawspan, Pearl Harbor, HI
Precast seat risers, double tees and stairs for Safeco Field – home of the Seattle Mariners
194′ long single-piece piles, deck panels, and sheet piles for Everett Homeport Carrier Pier and Breakwater Pier
Development in collaboration with WSDOT and PNW/PCI of new 7′ and 8′ deep Wide Flange Girders for long-span bridges
Widespread use of hollow core slabs for heavily loaded lids of large underground water detention vaults
North American licensee for Core-Loc shore protection elements
2000’s
13,000 pieces of curved single-pass tunnel liner segments for two tunnels in Seattle
58,000 sf of heavy duty marina floats for the City of Seward, AK
Construction of a Super-Girder plant; 30,000 sf enclosed facility with the capability of fabricating over 200 ft. long girders, a capacity of up to 4.4 million lbs of prestress force, and the ability to lift 150-tons
Collaboration with WSDOT and PNW/PCI for expansion of the Wide Flange Girder product line; capable of producing and shipping girders with span lengths of more than 230’
Production of an innovative and efficient modular hybrid floating pier (MHP) for the U.S. Navy; The MHP system takes maximum advantage of high performance light-weight concrete and various reinforcing products
2010’s
125 ft. long, 165-ton Hammerhead girders for Manette Bridge in Bremerton, WA
Trapezoidal girders for mass transit projects
Research, development and implementation of Self-Consolidating Concrete and Lightweight Concrete mixes
205 ft. long, WF100G girders for Alaskan Way Viaduct in Seattle, WA; the longest girders shipped via truck in the United States at the time
Fabrication of two, 20 ft. deep x 50 ft. wide, floating cruise ship berths for the city of Juneau, AK; totaling 35,000 sf
Rapid fabrication of 65” deep Decked Bulb Tee girders for a section of I-5 that collapsed into the Skagit River; use of Lightweight concrete mix to avoid modification of existing bridge substructure
2020’s
Constructed our new Mega-Girder plant; 25,000 SF enclosed facility with two beds capable of 6,000,000 pounds of pre-tensioning
Production of a 223’-4.5” long WF100G girder for the I-5 Portland Avenue project, giving it the title of world’s longest, single piece pre-tensioned girder delivered by truck.
Production of full-span precast concrete girders for use in elevated guideway sections of Sound Transit’s Link Light Rail mass transit system.
I built bridges. I broke test cylinders in college that came from the Sunshine Skyway Bridge that spans Tampa Bay.The cylinders were breaking 7000 PSI after 30 days underwater.Post tensioned cylinder piling 140′ 6′ I.D. 6″ wall.The concrete was blue-green color with the hardest dam crystalized lime stone you ever seen ! That was I-664 twin spans 3 miles long from Portsmouth,VA over to a man made island where the tunnel started.
@ΜΟΛΩΝ ΛΑΒΕ
Thanks for the explanation. I’ve read quite a bit about the Roman Republic and Empire, but never read the reason for the holes in the structures.